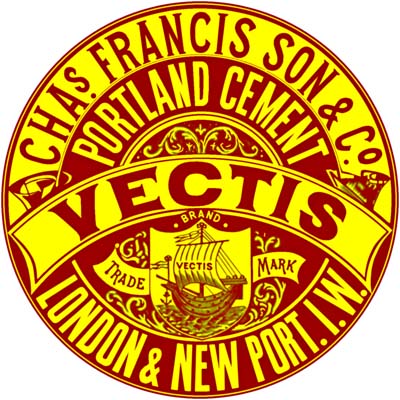
Charles Francis' Vectis Brand.
Location:
- Grid reference: SZ50519166
- x=450510
- y=091655
- 50°43'20"N; 1°17'4"W
- Civil Parish: Northwood, Isle of Wight
Clinker manufacture operational: 1852-1944
Approximate total clinker production: 2.2 million tonnes
Raw materials:
- Upper Chalk: earlier from Portsdown: 461650,106400, Portchester, Hampshire (Spetisbury Chalk Member: 78-80 Ma) and 463600,106600, Cosham, Hampshire (Newhaven Chalk Formation: 82-85 Ma): from 1870, partiallly supplemented with marl from Shide Quarry (Culver, Newhaven and Seaford Chalk Formations: 78-88 Ma) at 450600,88100, Arreton, Isle of Wight, by road; from 1897, entirely from Shide, by rail
- Alluvium from the Medina, the Hamble and Fawley: from 1895, Oligocene clay (Hamstead Formation: 28-31 Ma) was extracted from a pit at 450250,91750, and this became the exclusive source in 1913.
Ownership:
- 1852-1863 Charles Francis and Sons
- 1863-1900 Charles Francis, Son and Co. Ltd
- 1900-1944 APCM (Blue Circle)
Otherwise known as Dodnor Works or West Medina Works. The plant commenced about 1840 for manufacture of Roman cement, probably also making Frost’s “British cement”, the location being chosen, as with many other early plants, because of the availability of a tidal mill, the dam of which is at the south end of the site. Septaria for Roman cement were dredged from the Medina and from reefs off the coast of the Isle of Purbeck. Portland cement production began in 1852 or a little earlier. There were 18 wet process bottle kilns in 1866, not all of which may have been used for Portland cement. In 1882 four more were built. Between 1875 and 1897, chamber kilns were built in sets of two (60 t/week), five (150), two (60) and five (155). In 1902 a further block of six (130 t/week) was added, and a Schneider kiln, burning surplus slurry dryings. By this time the bottle kilns were disused and were demolished after WWI. It became one of only two plants (the other being Arlesey) outside the Thames/Medway area comprising APCM in 1900. The rotary kiln was inserted between the second and fifth blocks of chamber kilns, and all but the last block were allowed to fall into ruin. The last block was only used for top-up capacity, being last used in 1926. The plant was described in detail in the APCM 1924 schedule. The plant, which had supplied far-flung parts of Britain and the export market for which its water-only transportation was acceptable, became irrelevant as the industry established itself in the north and west, and raw material reserves were too slight to warrent a plant upgrade. The plant officially closed on 30/6/1944. Jackson says the kiln shut down in 1939, but John McDine argues convincingly that the kiln operated nearly until the plant closure date. The plant was on the Newport-Cowes railway, and used it for chalk haulage, but its cement distribution was almost exclusively by water, especially in its heyday, when it exported globally. The site became a depot for the Isle of Wight, taking in cement from Thames-side and Rodmell. The plant remained intact apart from the rotary kiln and has only recently been cleared for redevelopment. The small group of kilns at the SW end of the site are being cleaned up and preserved.
Power Supply
The plant originally used the tidal mill for finish grinding. Further power requirements and the washmills were supplied by steam engines driving though layshafts. The washmill steam engine was replaced with a gas engine around 1900. A generator driven by a 150 IHP triple-expansion steam engine was used to drive the rotary kiln section. During the late 1920s, the rest of the plant was electrified, with power from generators driven by gas engines. The power supply was finally switched to grid around 1939.
Rawmills
The plant always used washmills on the quay, fed with materials from barges. With the change to the harder IoW raw materials, chalk and clay were fed to three 80 HP rough mills, one 30 HP intermediate mill and one 10 HP screening mill. From the early 1930s, clay was milled in a separate washmill to an elaborate blending system holding two weeks' clay, then the chalk was washed with clay slurry in the rough-mill screener-mill combination.
One rotary kiln was installed:
Kiln A1
Supplier: Ernest Newell.
Operated: 1913-1944
Process: Wet: a calcinator was added in 11/1934
Location: hot end 450530,91651: cold end 450491,91658 (later 450483,91659): unenclosed.
Dimensions:
- 1913-1923 130’4” × 7’10½”B / 7’4½”CD (metric 39.73 × 2.438 / 2.248)
- 1923-1944 lengthened to 155’4” (47.35 m)
Rotation (viewed from firing end): anti-clockwise.
Slope: 1/25 (2.292°)
Speed: ?
Drive: ?
Kiln profile: 0×2400: 14503×2400: 14503×2248: 39726×2248 (later 47346×2248): tyres at 4877, 21336, 37795: turning gear at 24079
Cooler: rotary 40’1” × 6’4” (metric 12.22 × 1.930) beneath kiln
Fuel: Coal
Coal Mill: indirect: 2 Griffin mills. In the late 1920s, these were replaced with a Newell combination mill.
Exhaust: via dry drop-out chamber direct to stack: after the calcinator was installed, an electrostatic precipitator was added between the ID fan and the stack.
Typical Output: 1913-1934 103 t/d: 1934-1944 127 t/d
Typical Heat Consumption: 1913-1934 8.7 MJ/kg: 1934-1944 7.3 MJ/kg
Sources:
- Primary Sources:
- Greenhithe Archive
- APCM 1924 schedule
- Alan Dinnis, West Medina Cement Mill, Dodnor, Isle of Wight: a History, W. J. Nigh & Sons Ltd, 2016, ISBN 0950412635
- there is a remarkable video at the East Anglian Film Archive showing the quarries and plant in operation in the 1930s
- Ordnance Survey 1:2500 mapping
- BGS mapping and monographs
- Confirmatory Sources: